Planking an Adirondack guide boat is a challenge that can bring you to your knees. Planks on a guide boat follow a sinuous 3-D shape. Each new plank must fit precisely to the one that went before it. You can’t fake it. Many times I thought that I could just force one end or the other of a plank into fitting its mate and it would be OK. No dice. Its like 3-D wall paper. If you push one end of the plank to make it fit it causes a bulge somewhere else.
So I have now moved into my new shop and the new boat I am building is ready for the 5th round of planking (there are 8 rounds of planks on my boat). The 5th round is where things really get complicated. Just as the planks that went before number 5, this one must match up to the free edge of the preceding plank. But now we have arrived at the curve of the bilge. That is where the hull transitions from being roughly horizontal to being nearly vertical. The ribs are more curved here to accommodate that transition. The new plank must be shaped to fit the curvature of the ribs around the bilge.
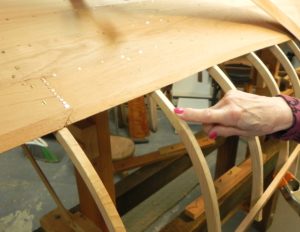
The old timers (and some new timers) got around this problem by hollowing out, or as they termed it backing out, the inward facing surface of planks in the bilge region. This requires a special plane with a convex sole. They started with a somewhat thicker plank to allow for the amount they would remove. To add to the complexity, the amount of the bilge curvature changes as one moves from midships to the stems.
Since I feel very challenged to try backing out a plank the old way, I use a method I call flash molding. It is used by instrument makers to shape the sides of the sound box of a guitar, for example. Flash molding involves wetting down the wood being bent, wrapping it in aluminum foil, heating it to around 300 degrees F, and clamping it to the shape you want it to take on. Heating is done using a thermal blanket. During the heating cycle the wood becomes very pliable and will take practically any shape you desire. The new shape remains permanent upon cool-down.
Here is the flash molding set-up used to shape a plank in the turn of the bilge region.
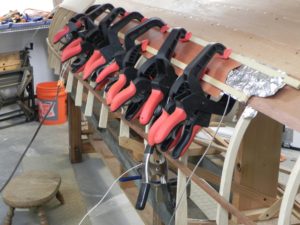
Flash molding worked great on one side of the hull. Those two planks picked up a nice shape that fit their mating ribs exactly. Not so on the other side. One plank just did not respond to flash molding. I even tried flash molding again. No luck. What was going on?
I remembered that flash molding works best when the plank is quarter sawn. When quarter sawn, the grain is parallel to the plank’s side edge edge. Quarter sawn planks bend more easily in a radial bend than in a longitudinal bend. This bend response is just the opposite of flat sawn planks where the grain is more or less parallel to the top and bottom surfaces of the plank.
I hated to give up on this plank. I had put a lot on work into it. I had shaped it to fit the previous plank (I thought) and cut the bevels on both edges. The final straw was when it just would not fit to plank #4. In fact it was nearly 1/2″ off on one end. See below:
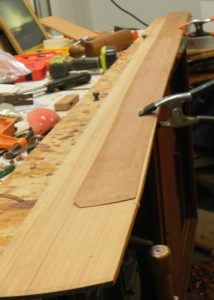
This reminded me of a tale Keith Austin told me about a guide boat he was building. Now Keith is the nephew of Bunny Austin. The Austins have been building wooden boats since the 1830’s. The Austin patriarch, William, lived on the north shore of Long Lake and would build about one boat a week and sell them for $15.
While building a guide boat Keith found that one of the planks he recently hung had cracked. He called Uncle Bunny to commiserate. Bunny could emphasize with Keith having experienced these sorts of setbacks more than once. Bunny told him “What you need son is a crying chair. You sit in the crying chair and gather yourself up to go back and try again”. Here is Bunny in his shop in Long Lake.
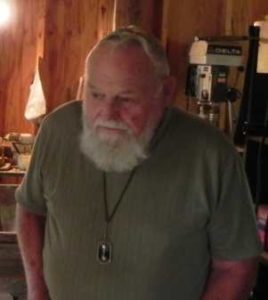
I learned that Bunny is quite a guy. He was a Marine Corp. pilot during the Cuban missile crisis and flew reconnaissance missions over the island of Cuba during that desperate time. I’m certain he wasn’t always sure he would be coming back from some of those flights, especially the low altitude ones. Bunny is an unsung hero in my mind!
Now I don’t have a crying chair but here I am crying over a plank that just didn’t make it.
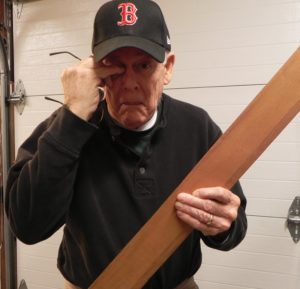
So after that set back I thought I would never finish round #5 of planking. Then I discovered I hadn’t installed the stitched ribs. More about that next time.